Pause, Reflect, Improve: Mid-Year QMS Essentials
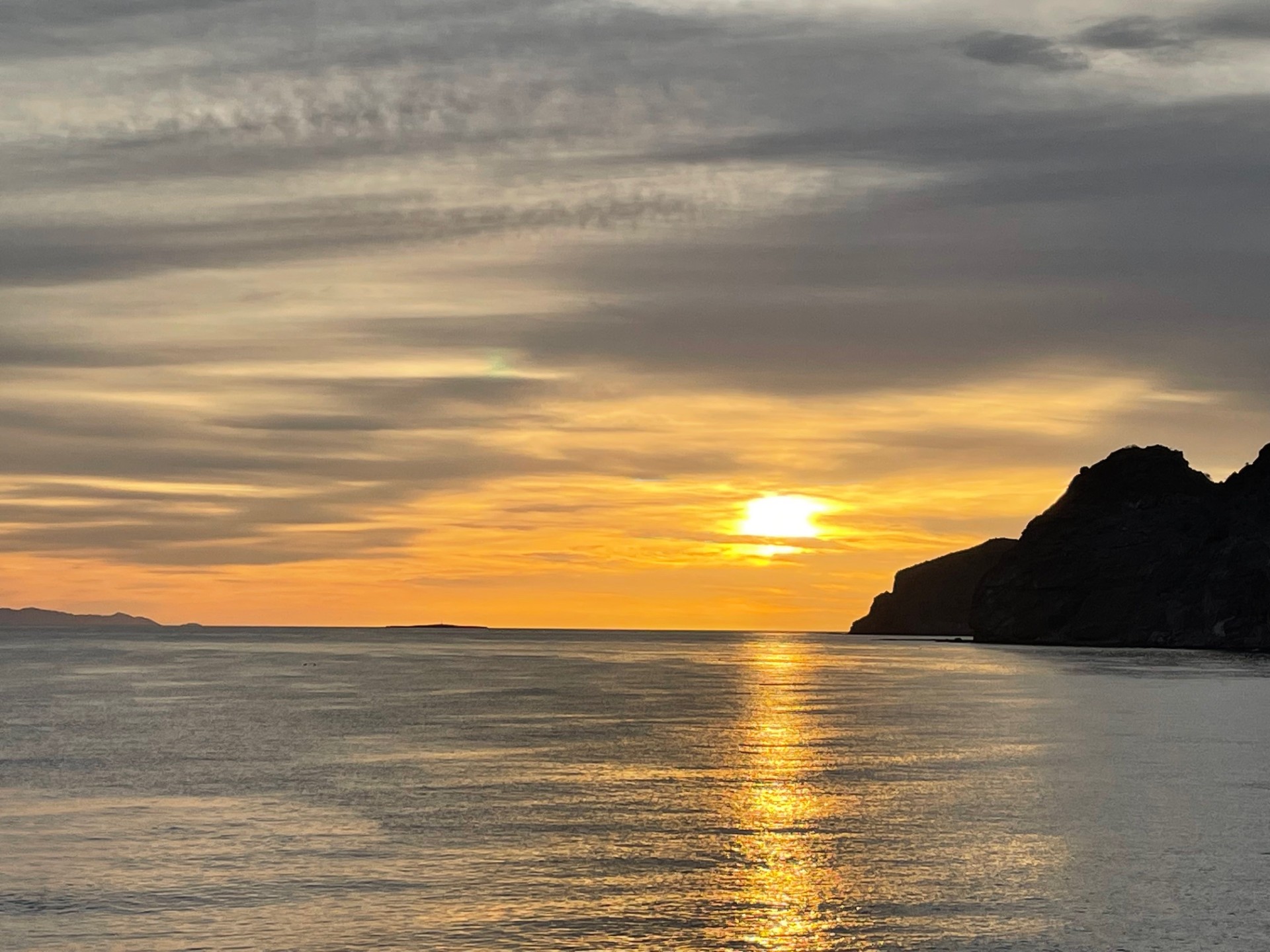
QMS Check Up
We’re halfway through the year! It’s time for summer vacations and easier commutes without the school traffic. It’s also the perfect time to hit pause and assess your Quality Management System. Are you on track with scheduled and required activities? Are you meeting your stated goals?
A mid-year review is an ideal opportunity to celebrate what’s working, identify what’s not, and make any needed adjustments before year-end pressures set in. Here are a few key areas to evaluate now to keep your QMS strong, optimized and audit ready.
Documented Information Status
It’s important to make sure that documented information is properly controlled and maintained. In our hectic work environments, it’s easy to overlook this task or push it down the priority list but delaying it can lead to employees having outdated or incorrect information. To avoid errors and confusion, conduct a document assessment.
- Are document reviews and approvals up to date?
- Are current versions available to employees?
- Have obsolete versions been removed or archived?
- Have changes been effectively communicated and implemented?
Internal Audit Progress
ISO9001 requires that audits be conducted at “planned intervals”. Those intervals are defined by you and are reflected in your audit schedule. Reviewing progress helps ensure you are on track. Keep in mind, conducting the audit is only part of the process. It’s also essential to communicate the results and maintain evidence that the audit was conducted.
- Have all audits been conducted and closed on time?
- Have results been communicated to the necessary people?
- Are any required notes, reports or other evidence completed?
- Have corrective actions been initiated where needed?
Corrective Action Progress
Identifying and initiating corrective actions is a vital part of any Quality Management System. These actions drive improvement and help prevent recurrence. However, initiating corrective action isn’t enough. Those corrective actions must be acted on to drive improvement and proper urgency needs to be assigned to keep corrective actions moving toward resolution.
- Are there any overdue corrective actions?
- Are root causes adequately identified?
- Do action plans address the root causes?
- Has the effectiveness of completed actions been verified?
Training Status
With ongoing changes in the labor market, a robust training program is essential to running a smooth operation. Ensuring employees have the needed skills and knowledge sets them up for success, keeps employees safe and ensures quality output.
- Are training records up to date?
- Is the training process effective?
- Are qualifications and assessments up to date?
- Are there any gaps that need to be addressed?
Moving Forward
These are just a few processes to get you started, but you should check other processes that require maintaining or that your organization struggles with. At a minimum, check your metrics or key process indicators, although ideally this is happening on a regular basis (You are checking regularly, aren’t you? I thought so!).
Other areas you may want to review are:
- Management Review
- Customer Feedback
- Supplier Performance
- Risk
Taking time to review progress now will give you time to make improvements to ensure your QMS stays on track and continues to support your goals for the rest of the year.